Manufacturing is a driver of economic growth around the world, particularly so now after the COVID-related disruptions at the start of the decade. As global supply chains evolve and technological advancements accelerate, manufacturing across the MEA (Middle East and Africa) has the potential to boost regional performance.
Economies are showing signs of transformation, adapting to the rapid technological advances of the Fourth Industrial Revolution.
Digital skills have the potential to be the catalyst for this transformation.
The business case for digital skills
Digital transformation is no longer a luxury; it is a necessity.
Companies which integrate digital competencies – such as data analytics, automation, artificial intelligence, and cloud-based collaboration – see improvements in efficiency, cost reduction, and market competitiveness. A report from McKinsey highlights how companies adopting digital tools in manufacturing achieve productivity gains, alongside increased agility, and innovation capacity (1).
Across the MEA, where manufacturing is a key pillar of economic diversification, governments and industry leaders recognise this. Initiatives such as Saudi Arabia’s Vision 2030 and the UAE’s Industry 4.0 strategy champion digital adoption.
Eighty per cent of companies in the wider MENA region are adopting digital technologies, and investment in digital transformation is predicted to rise rapidly (2). Examples of investment include the Saudi Advanced Manufacturing Hub strategy which, in partnership with the World Economic Forum, aims to increase the number of factories to 36,000 by 2035 (3).
Through the Make it in the Emirates campaign, the UAE is attracting some of the world’s leading technology and industrial companies to work within its manufacturing ecosystem.
All of this requires a workforce equipped a range of digital skills.
Bridging the digital divide
Worker profiles, job roles and the skills required in manufacturing are rapidly evolving. Traditional skills, once sufficient to operate machinery or manage production lines, are no longer enough. The modern manufacturing worker needs to be proficient in digital literacy, data analytics and machine programming. Indeed the World Economic Forum highlighted how 85 million jobs globally could be displaced by automation by 2025, but 97 million new roles could emerge—many requiring digital expertise (4).
In MEA, the challenge is twofold: preparing the existing workforce for digital transformation while ensuring new entrants have the right skills from the outset.
As technology continues to reshape the manufacturing industry, there is an urgent need to align education systems with industry demands – both to bring people into the sector and to up or re-skill those in the sector.
As it stands, not only is there a mismatch between the skills that workers possess and the skills employers require, there simply aren’t sufficient students graduating from university with the right skills.
When employers complain that workers do not have the right skills, they are reflecting on more than just education credentials or technical qualifications. Workers across the region may lack proficiency in critical areas such as digital literacy, data analytics and advanced manufacturing technologies, leaving them underprepared for jobs in modern factories.
As an example in Africa, 21% of business leaders reported that the lack of adequate skilled workers was a major constraint to their operations, with over 29% of production workers rated as unskilled (5).
From early education to technical training, students must be exposed to the skills that will prepare them for future careers in manufacturing. Increasing emphasis on STEM education is required to cultivate the next generation of engineers, designers, and technicians.
Investing in structured training programmes, apprenticeships, and industry-academia partnerships will be critical. Digital literacy must be embedded into technical and vocational education, and businesses must take a proactive role in upskilling employees through continuous professional development.
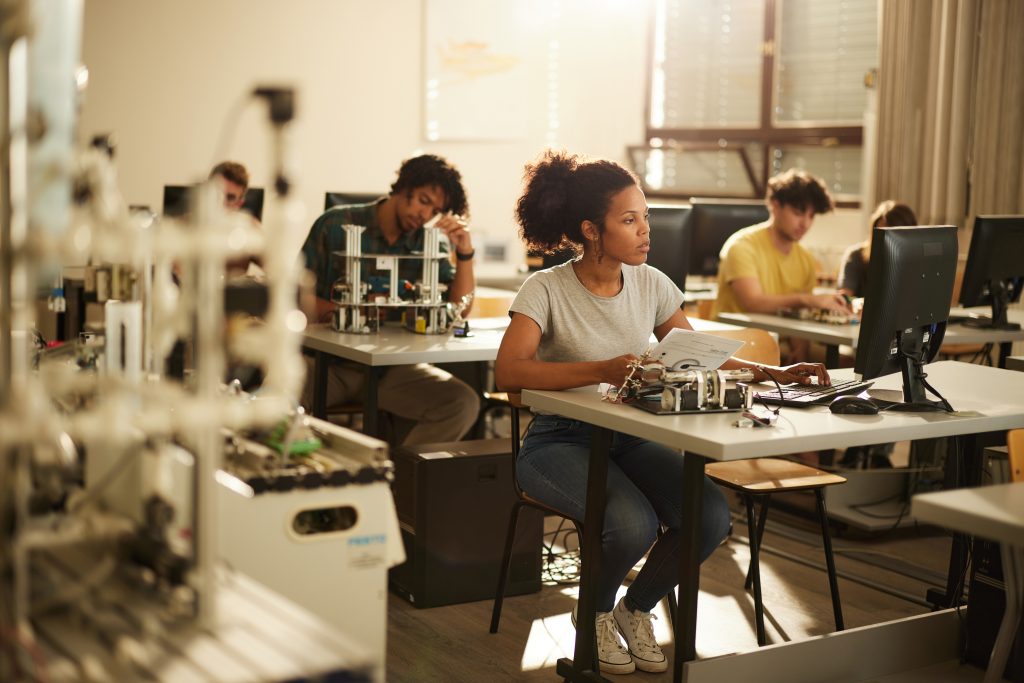
Economic and business growth potential
If the region invests in developing digital skills, it is my belief that MEA’s manufacturing sector will benefit:
- Enhanced productivity & efficiency – Digitally enabled operations streamline production, reduce waste, and optimise supply chains.
- Job creation & workforce development – While automation may replace some roles, digital adoption will create new, higher-value jobs, shifting workers from manual tasks to strategic, technology-driven roles.
- Increased foreign investment & market expansion – A digitally skilled workforce enhances investor confidence, attracting international partnerships and facilitating export growth.
- Resilience & adaptability – Digitalisation enables manufacturers to respond to market fluctuations, supply chain disruptions, and evolving consumer demands with agility.
For leaders, the message is clear: investing in digital skills is not just a workforce development initiative—it is a strategic growth driver.
Investing in skills across all ages not only delivers improved productivity and innovation now, it also builds the future workforce. A workforce which is resilient, flexible, and adaptable – with the right skills at the right time, in the right place.
Structural reforms and targeted policies are needed to make skills accessible and relevant, from foundational digital literacy in schools to advanced digital capabilities in the workplace. Not only does digital investment need to be incentivised, school and university curricula need to be aligned with industry demands.
Governments, academia, industry bodies, and businesses must collaborate to prioritise digital education, provide accessible training, and build an ecosystem where digital competencies become a cornerstone of industrial success.
What’s your role in unlocking digital growth?
In our latest report, Making for Tomorrow: Skilling Across the Ages, we explore the importance of investing in digital skills across the Middle East and Africa. We highlight the roles schools, universities and businesses need to play in building a new workforce to work in sectors shaped by advanced technologies. We talk about the importance of collaboration and the need for investment by governments and other regional stakeholders.
Tomas Karlsson is the sr manager of channel services at KnowledgePoint. This means he oversees the management of outsourced extended enterprise learning programs, recruiting, and supporting global network of training providers on behalf of organisations, including Autodesk.
- (1) The next horizon for industrial manufacturing: Adopting disruptive digital technologies in making and delivering. McKinsey, 2018
- (2) Tech Leaders and the next growth chapter. Accenture, 2021
- (3) Is Industry 4.0 Transforming the Middle East region’s manufacturing sector. The Fast Company Middle East, 2023
- (4) The Future of Jobs Report. World Economic Forum, 2020
- (5) Skills for Employability and Productivity in Africa (SEPA) Action Plan, 2022–2025. African Development Bank Group, 2022